CNC machines can be quite expensive, and they should be. They are complex machines often capable of the magical manufacturing duty of turning a piece of raw material into something more intricate with another purpose while maintaining extreme precision. The parts made on CNC machines are in every room of your home and business. Right under your nose right now, there are probably dozens of parts made on CNC machines, or at the very least parts that were formed using molds made by CNC machines.
Yep, CNC machines are kind of a big deal.
If you are shopping for or will be shopping for a CNC in the near future, this article is for you. If you already own one or more CNCs, this is also fairly relevant. It will shed some light onto the role options play in efficiently getting accurate and detailed manufacturing metrics from your equipment.
Scope of Knowledge
Okay now I need to confess, while I probably know a lot more about a CNC machine than the average person, I may know less than you. Especially if you are a seasoned advanced manufacturing business owner, manager, machinist, manufacturing engineer, or maintenance tech. I also will not pretend to understand your specific requirements without having discussed the topic with you directly at length. My area of knowledge and the source of my suggestion is based on my experience working with CNC communications and data collection. Or more specifically, on some of the obstacles I’ve seen businesses face while in pursuit of excellence. I am hoping that together we can learn from their mistakes and possibly save you large sums of money in the future.
Why Ethernet is Important for CNC Communications
Our customers have CNCs of all shapes and sizes, makes and models, ages and capabilities. While machines exist that do not need to receive new programs frequently, that is not typical. This means that we need to have a method to transport G-code programs to the CNC machines to operate. The easiest and best system for sending and receiving files on a CNC is via a wired Ethernet connection. Typically Ethernet connected machines run Windows on the control and use Windows Networking for file access. Some may also use NFS, FTP, or native protocols, the exact method doesn’t matter*. What does matter is that with Ethernet your machine communications will be fast, reliable and simple to configure. Without Ethernet there are significant limitations.
*The protocols for Ethernet could matter if your communications software doesn’t support them, DNC-Max supports every production communication method available.
Even if your machine is programmed on the floor or doesn’t need to have new programs loaded so communications aren’t an issue, would you still like to know how efficiently it is working for you? How long it actually take to make a given part? Where you stand vs Industry standards like Overall Equipment Efficiency (OEE)? If so, read on…
Automatic Machine Data Collection
When it comes to collecting data from a CNC, which is predominantly knowing if the machine is running or not, an Ethernet port is usually required. This has to do with  the fact that automatic data collection, or the automatic reading of detailed data about what the machine is doing and how it’s doing it. This data acquisition is, for practical purposes, dependent on Ethernet connectivity. CNC machines that support automatic data collection from day they are put into service are incredibly simple to setup and offer vastly more information than any other practical data collection method.
Depending on the technology, with automatic data collection we can find out things like:
- Cycle Start/Stop
- Part Complete
- Feed Hold
- Alarm
- Ready
- Feed Rate
- Rapid Rate
- Spindle Rate
- Mode
- Current Program
- Detailed Alarms
- Spindle Load
- and more…
To perform quality automatic data collection your CNC control will also need some kind of data collection standard. These are specific to the machine tool and controller manufacturer. These are systems such as Fanuc FOCAS, MT-Connect, Haas M-Net, Heidenhain Opt18, Siemens Netlink Pro, Brother HTTP, or Mitsubishi M700/800. We also require a system like CIMCO MDC-Max that is able to decipher and analyze those protocols into visual live screens, reports, OEE calculations and to allow for operator input for things that can’t be automated such as tooling, setting, breakdown, etc. Each collection standard is unique, and that is worthy of it’s own article. For now you can’t go wrong with any of the previously mentioned systems, because they all provide decent capabilities. While shopping for new equipment be sure to ask your machine tool vendor what messages will be available with your specific perspective new machine. For what it’s worth MTConnect and Fanuc FOCAS are exceptional and widely used, they go a bit farther than some of the others.
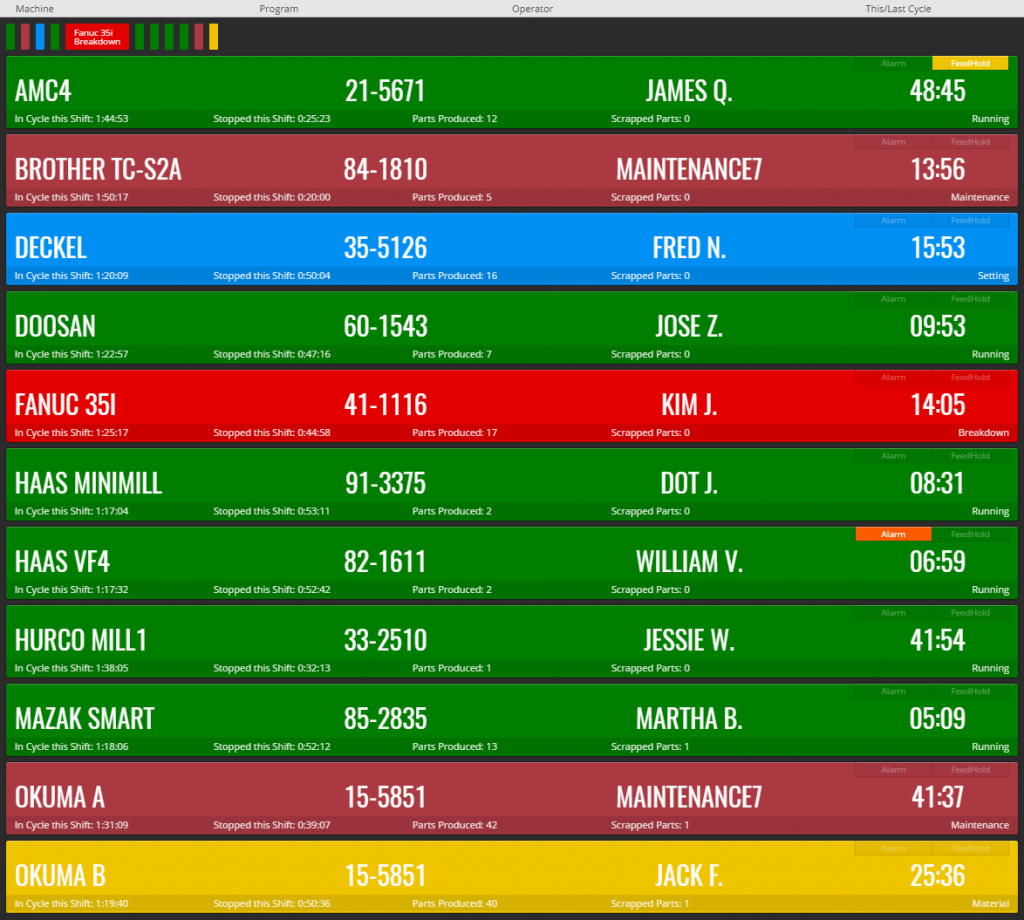
An example Live screen – CIMCO MDC New Web Client – Managed Solutions Color Theme. Cycle status, Job, Alarm Status, Feed Hold, Parts Produced are all examples of automatically collected data. Maintenance, Breakdown, Setting, Scrapped Parts and Material are based on user input. Live screens are typically located on the shop floor and anywhere individuals responsible for production are located.
What to do if you own a machine without the Ethernet and/or Data Collection Protocol Option
The first step is to determine if that machine is worth the trouble. For example if you already know that it is only good for certain jobs and they represent a small amount of the parts you produce, then it might not be worth the expense and time involved. Unless of course you need to come up with some hard numbers in order to justify to your management that the machine needs to be replaced.
For productive machines the first step is to find out if there is an OEM upgrade for it. Get in touch with your machine tool vendor and ask them what your options are to add data collection and Ethernet based communications support to your machine. In some cases a kit is available, or maybe they just need to take some money and flip that magical option switch to enable them. Either way if they can add support for one of the collection standards I mentioned earlier (e.g. FOCAS, MTConnect, Haas M-Net, etc.) without breaking the bank, that’s going to be your best bet. I’ve seen where this was as little as $350 upwards to $4,000. If the option seems pricey (say more than $2,000 all in), there may be other options that will be adequate to calculate OEE and give you the bare necessities – count cycle time, parts completed, feed hold and basic alarm status (on or off).

Prepping to buy that CNC
While there are ways to retrofit and adapt a machine, hopefully you now agree that it really does make sense to add “supported data collection protocol and Ethernet port” to your list of must-haves. If you can’t agree to that, at least ask for a price with the option now and how much to add it later, and if it is even possible. The relative small amount you will save leaving these options off may come back to haunt you in the future when you do get around to implementing machine data collection or when you go to sell the machine to upgrade. Besides, shouldn’t actual equipment effectiveness factor in the decision to replace or add a new machine anyway? 🙂
I navigate these types of situations frequently with our customers and would be happy to discuss your project. We also have partners in the industry who offer some exceptional solutions to help you get more out of the machines you already have including retrofits and options. Call me at +1 925-272-0384 or use our contact page to get in touch.